Pushing the Limits of Two-Phase Injectors with HPC
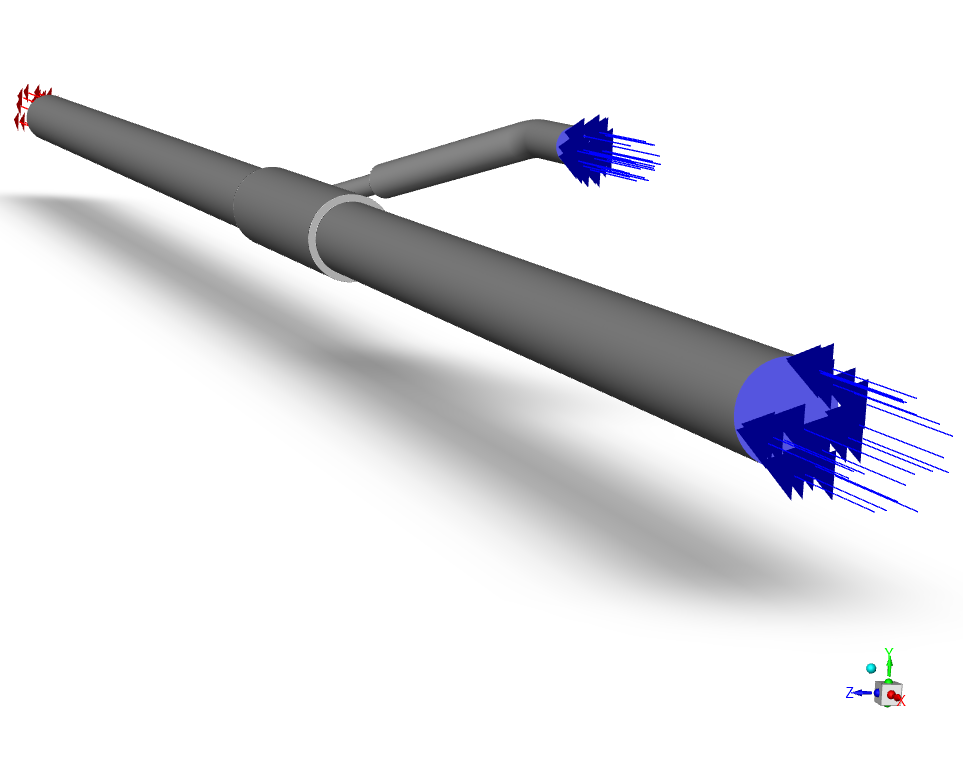
In the world of advanced cooling and heat transfer systems, two-phase injectors are gaining traction for their ability to efficiently mix vapor and liquid to enhance pressure recovery and energy efficiency. These systems, crucial in aerospace and industrial applications, depict the direct contact between a high-speed vapor jet and a subcooled liquid to induce condensation and improve performance.
Camila Braga Vieira, a researcher at Cenaero, tackled the complex challenge of analyzing these injectors through high-fidelity Computational Fluid Dynamics (CFD) simulations. Her work, in collaboration with Calyos, focused on understanding the intricate interactions between vapor and liquid flows inside an injector, particularly how key parameters—such as injection angle, working fluid properties, and entrainment ratio—affect overall efficiency. One considered injector geometry is the one depicted in the picture above.
The Power of HPC in Simulating Extreme Conditions
Conducting precise computational fluid dynamics (CFD) simulations of two-phase flows presents a significant challenge. These simulations require solving the three fundamental conservation equations: mass, momentum, and energy. The challenge lies in capturing the highly dynamic nature of the mixing region, where phase changes occur.
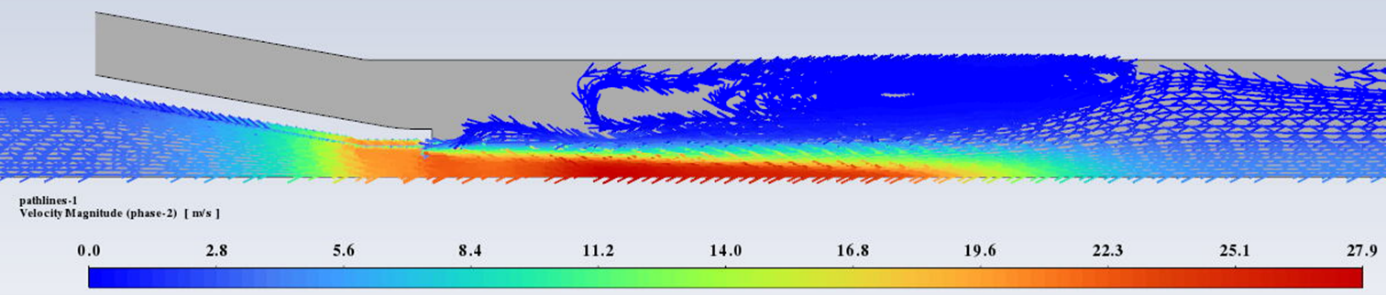
HPC played a crucial role in tackling this complexity. Camila used Lucia, the Tier-1 Walloon supercomputer operated by Cenaero, to perform these demanding computations.
With the power of Lucia infrastructure, complex 3D meshes are generated in less than an hour, allowing up to three full simulations per day.
Her simulations relied on the finite volume method, a numerical technique well-suited for solving fluid dynamics problems with high accuracy. However, achieving numerical convergence was a major hurdle—fine-tuning the model required extensive investigation of proper numerical methods to ensure stable solutions.
Bridging Simulation and Experimentation
One of the critical aspects of my research was ensuring that the numerical simulations are aligned with real-world feasibility.
By collaborating closely with Calyos, leading expert in two-phase cooling solutions, her work also could be validated at the experimental level. The project’s ultimate goal is to improve the performance of these injectors for practical applications, including aeronautics, where factors like acceleration forces and vibrations introduce additional design challenges that are yet to be fully explored.
Camila Braga Vieira

Camila is a researcher specializing in computational fluid dynamics. She holds a degree in industrial chemistry and a PhD in nuclear engineering. She pursued postdoctoral research at SCK CEN in Belgium, followed by another postdoc in CFD at the University of Sherbrooke in Canada. Now at Cenaero, she focuses on numerical modeling of different design aspects, including two-phase flows, contributing to advancements in injectors and heat transfer systems.