The Role of High-Performance Computing in Ensuring Nuclear Reactor Safety
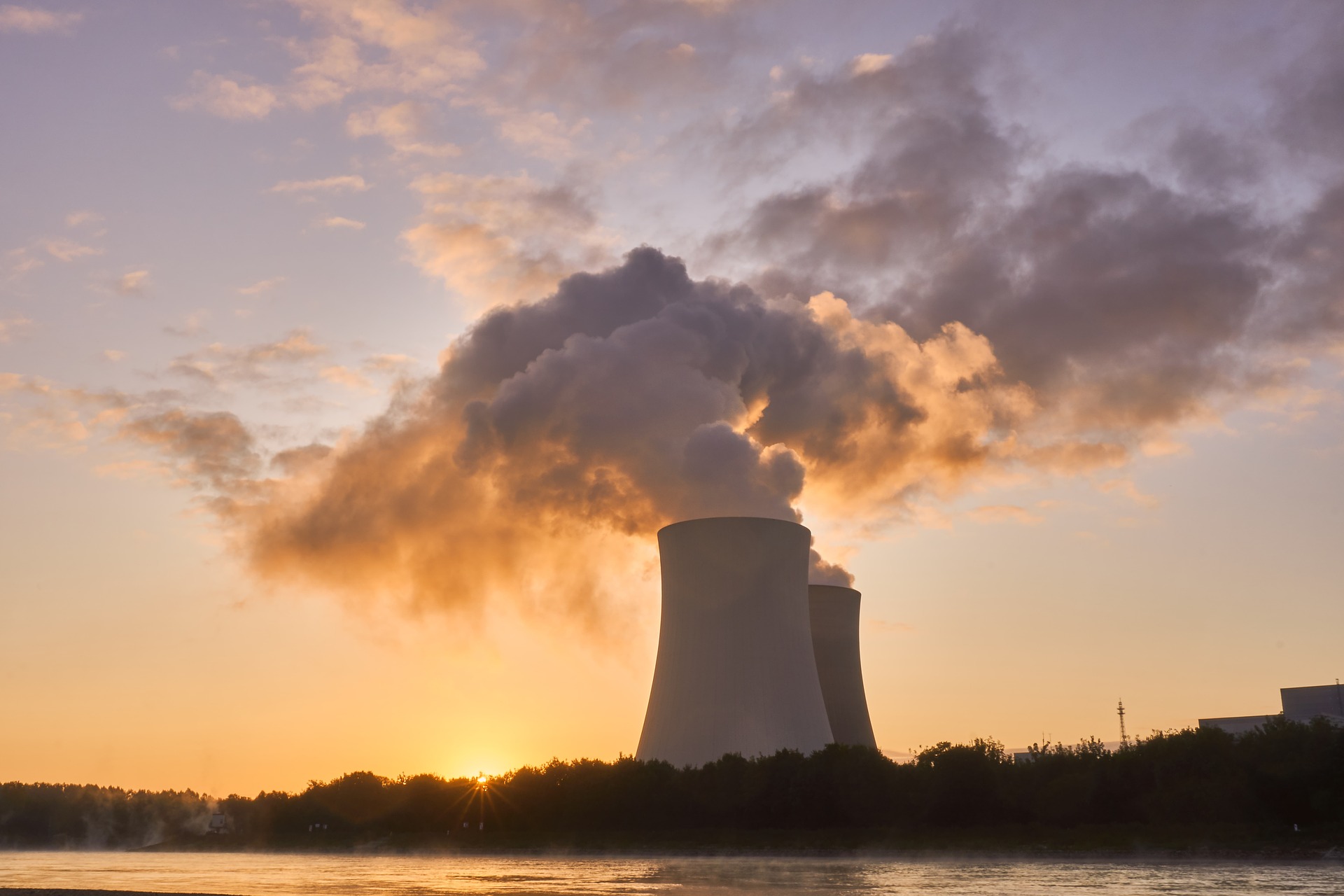
French version available here
Published on 06/02/2023
“Cracks” in a nuclear reactor?
In 2012, the federal agency of nuclear control of Belgium (FANC/AFCN/FANK) reported defects in the vessels of the nuclear reactor Doel 3 and Tihange 2. During planned maintenance, an ultrasound inspection of the wall of the nuclear revealed that the steel walls from the nuclear reactor vessel contained bubbles of hydrogen. It is believed that these bubbles were caused by an excess concentration of hydrogen during the steel manufacturing process. These bubbles were flattened during the forging of the steel for the nuclear vessel, resulting in bubbles with a length of about 15 mm while being thin as cigarette paper. [1]
Valéry Lacroix (Tractebel): “To evaluate the structural integrity of the vessels, these inclusions have been considered as "cracks" which is the worst case possible. “
Numerical simulation to assess the risk
Several experts and organizations have been consulted in order to determine whether these reactors could be safely restarted. A collaboration between Tractebel, a subsidiary of Engie providing engineering services, and Cenaero also emerged.
Valéry Lacroix: “Among a lot of analyses, numerical simulation has been chosen to assess the risk level. Due to the number and proximity of the cracks, such computation required HPC resources.”
The computations were performed using a software developed at Cenaero, “Morfeo Crack”.
Valéry Lacroix: “The first ones started with a limited number of simultaneous cracks and this was then increased. Such configurations required much caution to perform the computation within the available hardware resources while satisfying high-quality standards in the results. At this time, the amount of memory on the biggest available nodes limited the mesh sizes. Moreover, Cenaero developed methodologies to face the number of configurations and the post-processing operations to be carried out. ”
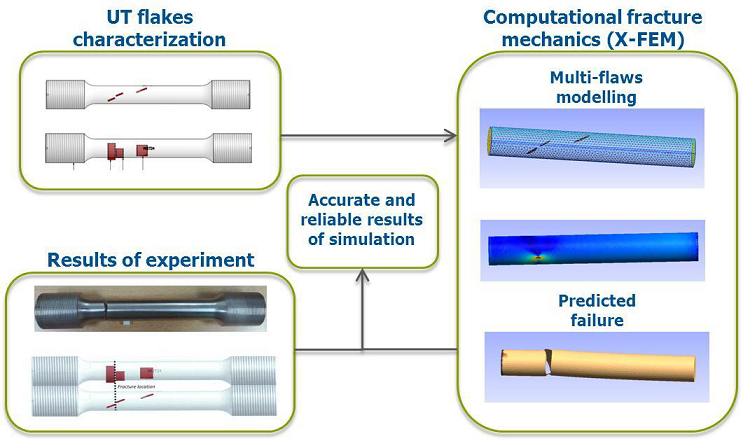
These numerical investigations helped in the assessment of structural integrity. Combined with inspections and other analyses, they led to the conclusion that Doel 3 and Tihange 2 could be safely restarted.
A successful collaboration
The collaboration on crack analysis between Tractebel and Cenaero is considered a success and still goes on with significant extensions. Recent works dealt with lifespan assessment by numerical simulations considering residual stresses due to the welding process.
From a scientific point of view, the specific needs of Tractebel helped Cenaero to improve the usedmethodologies and tools.
Valéry Lacroix: “Some work was carried out to extend computation to elastic-plastic fracture mechanics hypothesis. Moreover, the hardware limitation has been overcome by developing an adapted methodology, ensuring that computation on more than one node is possible which the same accuracy”
From a business perspective, Tractebel has acquired Morfeo Crack's software licenses to conduct its own analyses on various parts of nuclear power plants. Since then, Tractebel acquired unique expertise in this field that it can make available to its partners.
Simulations on supercomputers
These simulations were highly computationally demanding. A single computation required a high quantity of memory (up to 128Gb for the first computations). Due to the high number of configurations to compute (some hundreds), combined with the memory needs, the use of HPC infrastructure was a requirement.
Valéry Lacroix: “Some tests proved the capacity to exceed the memory limitation and used up to 768Gb. Such an amount of memory is not accessible without an HPC facility. “
Moreover, the software used to assess crack propagation risks is developed by Cenaero, which ensured a high reactivity and flexibility regarding the software needs.
Dr. Valéry Lacroix received is PhD from the Yokohama National University.
He was working as Research Engineer from 1999 to 2003 in Computational Mechanics at Université Libre de Bruxelles and as Design Engineer from 2003 to 2008 for Cenaero (Aeronautics) in Fatigue and Fracture Mechanics analyses.
Chief Engineer and Global Expert for ENGIE Group, he has been working in the nuclear sector since 2008 for Tractebel. He was first Design Engineer engineer carrying out mechanical calculations and flaw justifications for pressure components. As Principal Engineer he was in charge of the flaw as-sessment and the technical coordination in the Safety Cases of Doel 3 and Tihange 2 RPVs contain-ing hydrogen flakes. As Chief Engineer he is working on the calculations and the coordination of several EDF projects : Replacement of Primary Elbows (900MWe), Replacement of PRIS (1300 Mwe). Besides the technical projects, he is in charge of R&D program in Fracture Mechanics for Tractebel and is author of more than 50 scientific papers.
Meanwhile, Dr. Valéry Lacroix is member of different ASME Working Groups on Flaw Evaluation and on Reference Curves. He is member of the ASME Codes and Standard Technical Committee and Technical Program Representative of the ASME PVP conference.